The reason why centrifugal glass wool can absorb sound is not due to the rough surface, but because it has a large number of tiny pores and holes that communicate with each other. When sound waves are incident on the centrifugal glass wool, the sound waves can enter the interior of the material along with the pores, causing vibration of air molecules in the voids. Due to the viscous resistance of the air and the friction between the air molecules and the pore wall, the sound energy is converted into heat energy and is lost. The centrifugal glass wool has better sound absorption performance in the middle and high frequencies of sound. The main factors affecting the sound absorption performance of centrifugal glass wool are thickness, density and airflow resistance. Density is the weight per cubic meter of material. Airflow resistance is the ratio of air pressure to air velocity on both sides of the material per unit thickness. Airflow resistance is the most important factor affecting the sound absorption performance of centrifugal glass wool. If the flow resistance is too small, it means that the material is sparse, air vibration is easy to pass through, and the sound absorption performance is reduced; if the flow resistance is too large, it means that the material is dense, the air vibration is difficult to pass in, and the sound absorption performance is also reduced. For centrifugal glass wool, the sound absorption performance has the best flow resistance. In actual engineering, it is difficult to measure the airflow resistance, but it can be roughly estimated and controlled by thickness and bulk density. Glass wool manufacturer shares with you.
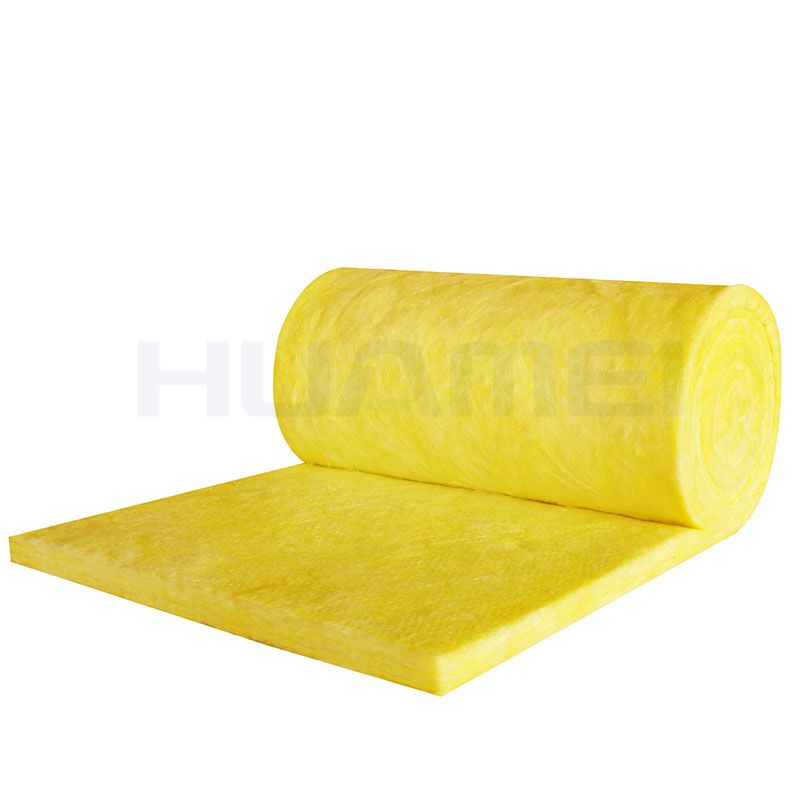
1. As the thickness increases, the mid-to-low frequency sound absorption coefficient increases significantly, but the high frequency does not change much (high-frequency absorption is always greater).
2. The thickness remains unchanged, the bulk density increases, and the mid-low frequency sound absorption coefficient also increases; but when the bulk density increases to a certain degree, the material becomes dense, the flow resistance is greater than the optimal flow resistance, and the sound absorption coefficient decreases instead. For centrifugal glass wool with a thickness of more than 5cm and a bulk density of 16Kg/m3, the low-frequency 125Hz is about 0.2, and the medium-high frequency (>500Hz) sound absorption coefficient is close to 1. When the thickness continues to increase from 5cm, the low-frequency sound absorption coefficient gradually increases. When the thickness is greater than 1m, the low-frequency 125Hz sound absorption coefficient will also be close to 1. When the thickness is constant and the bulk density increases, the low-frequency sound absorption coefficient of the centrifugal glass wool will also continue to increase. When the bulk density is close to 110kg/m3, the sound absorption performance reaches the maximum value, which is close to 0.6-0.7 at a thickness of 50mm and a frequency of 125Hz. When the bulk density exceeds 120kg/m3, the sound absorption performance declines because the material becomes dense, and the mid-high frequency sound absorption performance is greatly affected. When the bulk density exceeds 300kg/m3, the sound absorption performance is greatly reduced. The thickness of the sound-absorbing glass wool commonly used in architectural acoustics is 2.5cm, 5cm, 10cm, and the bulk density is 16, 24, 32, 48, 80, 96, 112kg/m3. Usually use 5cm thick, 12-48kg/m3 centrifugal glass wool. The sound absorption performance of centrifugal glass wool is also closely related to the installation conditions. When there is an air layer behind the glass wool board, the sound absorption effect is similar to that of a glass wool board with no air layer of the same thickness. In particular, the mid-to-low-frequency sound absorption performance will be greatly improved compared to the material actually attached to the hard bottom surface. The sound absorption coefficient will increase with the thickness of the air layer, but the effect is not obvious after increasing to a certain value. Use glass wool of different bulk density to stack together to form a form of gradually increasing bulk density, which can obtain a greater sound absorption effect. For example, the sound absorption effect of stacking a layer of 2.5cm thick 24kg/m3 cotton board and a layer of 2.5cm thick 32kg/m3 cotton board is better than a layer of 5cm thick 32kg/m3 cotton board. The 24kg/m3 glass wool board is made into a 1m long cross-section with a triangular shape, the surface density of the material gradually increases, and the average sound absorption coefficient can be close to 1.
评论
发表评论